个人观点是比亚迪的哪个方案太激进,太极端了。最近写的好几个回答都涉及到这个。最新的文章如下:
NEV-Futurist:再谈“刀片”电池
一、前言
最近写了涉及到比亚迪“刀片”电池的文章,引来比亚迪粉丝的一通指责,各种神奇说法扑面而来。所以还是想澄清一下自己的一些观点。
1.股市、车市、电池技术领驭三者相关,但也差异非常大,甚至有时候几乎没有关系;关注比亚迪股市的读者,您只需要看见比亚迪这次的话题很成功,汉很有可能会跻身成功B级车之列,存在与Model 3抗衡一下的可能性就可以了;
2.准备购买新能源车的读者,您最好等“汉”推出并发送到4S店,再综合考虑;
3.电池领驭的读者,笔者的观点是不看好“刀片”电池,或者说“刀片”不一定是很多电池/车企的最佳解决方案。
我的理由有以下几个方面,接下来一一介绍。
首先,明确一下几个前提:
1.磷酸铁锂电池将成为乘用车领驭的重要解决方案之一,下图是我对近几年BEV乘用车领驭差异体系应用的预估。(三个曲线区别代表2019、2022和2025)

2.磷酸铁锂用于乘用车,在铝壳领驭,最好是做成无模组方案即“CTP技术”,尤其是中低端的车型;
3.“刀片”的解决方案,不一定是铝壳磷酸铁锂电池领驭最优的,或者说性价比最高的方案;另外圆柱、软包电芯也是在发展的,不一定就被淘汰了(关于封装形式的问题,可以看一下下面这个文章)
二、本质是PACK空间利用率的优化
不管是把电芯做成“刀片”还是“板砖”,都是为了提升活性物质在电池包内部的空间占比。一般的电池包都是扁平型的,以大众的MEB平台为例,电池包就是一个大平板(被称作“巧克力”型),高度大概是120mm。在这种电池包里,电芯做成长条型,两端出极柱(类似“刀片”电池),是在高度上空间利用率很高的一个方案。

对比一下以下A和B两种形状的电芯。


假设A和B两种电芯都采用无模组的设计方案,用于同样尺寸的电池包,再假设电池包六个边壁(上下前后左右)到电芯取的尺寸是一致的(其实也是这样)。
那么A在高度方向上的空间利用率要差不少,因为本来电池包的高度就比比较小,A中不仅极柱和汇流排要占空间,内部的极耳也要占空间,整体下来大概得占25mm的空间,基本上有20%;而如果用B型的,假如B的长度是500mm,那么两端极耳、极柱和汇流排占的空间可能只有10%,这就提升了5-8%的空间利用率(B型在高度上不是完全不占空间,如果“刀片”做成1米长,那么就能提升大概10-15%的空间)。
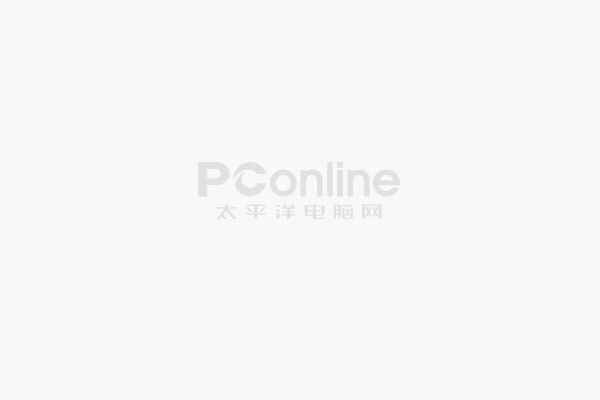
虽然目前大部分紧凑型以上的新开发纯电动平台的车型,其电池包都在向“巧克力”型发展,但是并不是所有的车型的电池包都是这样。举个极端的例子,神车公司的宝骏E100就不用。这也是我为什么说“刀片”不一定是最优方案的原因之一。
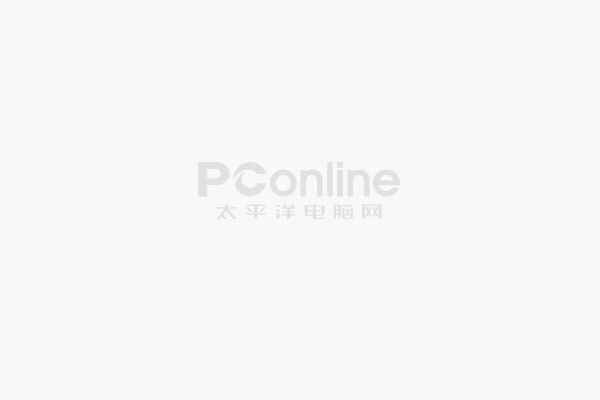
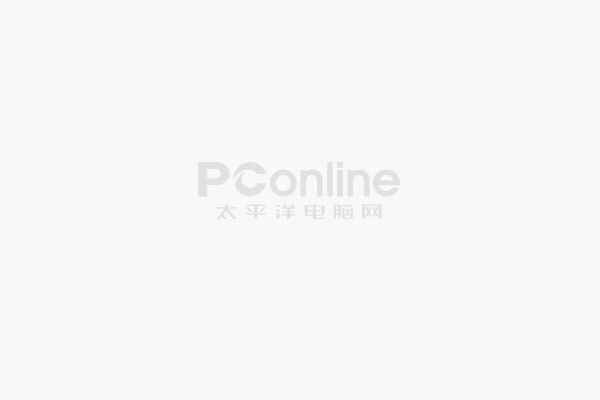
三、需要考虑加工工程和产品设计的综合匹配
对于“巧克力”型电池包,“刀片”电池是一种比比较好的方案,因为理论空间利用率高,能一定程度上提高体积能量密度,这是业内的共识,也是无数电池人共同努力的方向之一。但是现在就开始做“刀片”的话,一定是最好的方案吗?因为理论上的最佳方向,不一定是真正能够商业化的方向,我们的电池技术是在多种因素下,相互推动和妥协中,逐步发展的,其路线也是在不断创新中变化的。
笔者认为,目前往“刀片”方向发展,不管是做成一个1米长的3.2V电芯,还是内部做成几串进行升压(例如3串),都不是一个很好的方向。
首先是内部串联升压的方案,这个方案内部的卷芯还是那么个极耳,就不如几个短电芯(比如“刀片”减为0.5m)再外部串联了,可能会多出两个极柱和极耳的尺寸(50mm,相对1米是5%),但是工艺难度会大大降低,又不用考虑内部密封的问题,而这5%从其他方向找补回来还是比较简单的。
其次是直接做成一个3.2V电芯的方案,工艺难度会很大,另外不一定就能真正提升体积能量密度,原因如下:
1.从工程难度的角度来说,主要有以下几个方面(个人能够想到的):
1)极芯加工,如果是卷绕式的,那么1m长的极芯的卷绕对齐度、平整度和合格率,是难度比较大的;如果是叠片式的,那么也会遇到1m长极片的切片、转运,以及叠片对齐度等问题(SKI和LG在500mm长度软包电芯的叠片已经努力了很久,目前才看见实现的可能,但尚未推出批量产品);
2)电芯两端的厚度控制,化成排气问题,以及循环后期的两端膨胀一致性的问题等;
3)激光焊接、注液、分容等设备,如果要适应这么长度的电芯,基本上需要重新设计加工,基本相当于重建产线;
2.从另外的角度讲,不一定能够有效的提升体积能量密度,举个简单例子,在电芯加工过程中有一个重要的工序叫做“辊压”,目的是把活性物质通过外力进行压缩,减小相互之间的孔隙,以在相同厚度下放入更多的活性材料。显然,这种极片宽度越大,就越难压的更薄,越难压成一致的。如果降低压实密度,那内部的电量就会相对变少,反而空间利用率又低了一些。
类似的点还有很多,比如极片太宽,就要适当的增大隔膜包覆负极片,负极片包覆正极片的公差,也会降低实际的空间利用率;
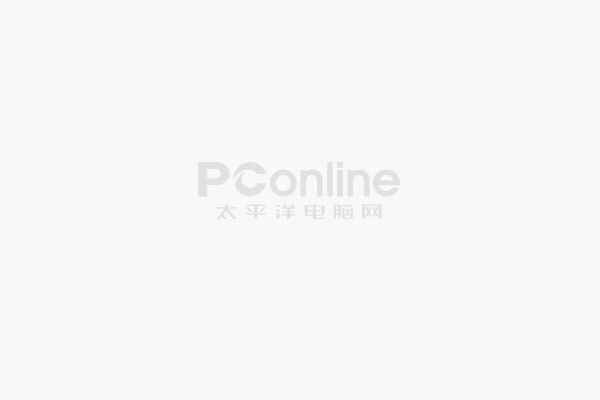
反而有些其他企业,逐步从部分工序改善,提升空间利用率,综合提升体积能量密度,这样反而来的更稳妥也更可靠一些,实际上的效果也可能会更好一些。比如MEB尺寸的电芯,或者LG、SKI的软包做成MEB电芯,或者从材料角度开发更高能量密度的正负极材料,等等,多种因素相互匹配,笔者认为才是产品设计的核心。
四、总结
笔者不是比亚迪黑,也不是不想他们做成,反而他们如果真的做出了对行业有突破性的创新,笔者是很乐意去学习的。
但是产品设计的关键在于综合多个因素的匹配,而不是一种要素设置为极限,其他要素为了这个极限而不得不舍弃很多东西。所以,笔者更希望比亚迪能够稳步前进,逐步发展,比如e6的电池是410mm长,那“汉”就做成500或者600mm,再下一代做成700或者800mm,而不是从410mm一次性跳跃到1m。
一个大型企业的优势在于能够多个方向相互协作、匹配,做出更适宜于目前技术现状的最优方案。但往往也会跑偏,一个方向的“霸权”,推动其他方向去大跃进,以致整个企业产品方向的错误,而导致巨大的损失。
前有马斯克的“无人工厂”的前车之鉴,后不希望王传福“刀片”后来之陨。创新是好的,盲目创新是要命的。
仅为一家之言,蚍蜉难撼大树,“迪粉”勿喷。